SONICGAUGETM
WIRELESS MONITORING SYSTEM
- Multi-year real-time downhole data acquisition system for field-scale digitalisation
- Fully wireless technology with no wellhead penetrations or downhole cables
- Compatible with production, injection, and observation modes
- 170+ years of accumulated monitoring time globally from 400+ installations
OVERVIEW
The SonicGauge™ Wireless Monitoring System is a state-of-the-art, real-time downhole data acquisition technology designed for seamless, plug-and-play deployment. It provides operators with real-time downhole pressure and temperature data for well-testing campaigns and long-term monitoring across the entire well lifecycle. The system delivers continuous data streaming during the production, injection, and observation (no-flow) phases.
SonicGauge™ sensors and SonicRepeater stations can be externally mounted on the tubing or retrofitted via slickline or e-line inside tubulars from 2-3/8” to 9-5/8”, using the patented Barracuda™ HEX-Hanger™. This compact 1.31” OD technology ensures minimal flow restriction (<3 psi across the toolstring) and does not require a nipple profile.
The SonicGauge™ Data Logger stores and transmits the acoustic data packets received wirelessly from the downhole sensors. Using an ATEX-rated accelerometer, magnetically attached to the wellhead, it eliminates the need for wellhead ports or penetrations. The data logger can be installed in control cabins, RTU cabinets, or operated independently via a solar-powered module.
From any field location, operators can access real-time well data via Modbus, Ethernet, 3G/4G, LoRaWAN, or Satellite, providing a standalone, field-scale digitalisation solution for remote monitoring and decision-making.
- Field-Scale Digitalisation for O&G, UES & CCS
- Retrofittable by Slickline in 2-3/8" to 9-5/8" Tubulars
- Monitor Injection, Flow & Observation Phases
- User Configurable Data Rates Post-Installation
- Multi-Zone & Gradient Data Included
- Real-Time Assessment: IPR, FCM, VLP, RTA & PTA
- Global Downhole-to-Desktop Connectivity
- Communication Through & Across Barriers
APPLICATIONS
The SonicGauge™ is a plug-and-play solution that delivers continuous real-time downhole pressure and temperature data, supporting Inflow Performance Relationship (IPR) updates, Vertical Lift Performance (VLP) curve analysis, Pressure Build-Up (PBU) operations, and dynamic reservoir modelling for green and brownfield assets. By providing uninterrupted well data, the SonicGauge™ helps operators reduce forecasting uncertainty, lower production costs, and support key investment decisions.
The SonicGauge™ can be permanently deployed on clamps or ported subs along the tubing during well completion or retrofitted inside the production tubing using the Barracuda™ HEX-Hanger™ via slickline or e-line. SonicRepeater stations, each equipped with onboard pressure sensors, provide real-time flowing and static pressure data from both the tubing and annulus, allowing engineers to monitor pressure gradients and multiple zones, fluid contacts, gas lift injection points, and ALS intake/discharge pressure—delivering critical insights for optimising well and reservoir management.
The SonicGauge™ can be retrofitted via slickline in injection wells, delivering real-time injectivity index data throughout the lifecycle of water flood and gas injection projects. In observation wells, it enables continuous pressure response monitoring, allowing operators to assess re-pressurisation trends accurately and track project success under shut-in conditions.
At field scale, the SonicGauge™ provides operators with critical input for the digital oilfield, enabling the simultaneous monitoring of all wells in flowing, injection or shut-in conditions for enhanced decision-making and reservoir management.
Installed well in advance of a well test programme, the technology ensures that steady-state conditions are established before shut-in or production adjustments occur, enhancing the accuracy and reliability of test data.
Permeability and skin can be estimated through Pressure Build-Up (PBU) analysis, which requires high-frequency data—from early-time wellbore storage effects to steady-state conditions. When acquired in real time, Pressure Transient Analysis (PTA) of PBU responses can be conducted concurrently, minimising production deferrals and optimising reservoir management decisions.
In DST applications, the SonicGauge™ delivers real-time surface-read-out data from below the tester valve, enabling live well test analysis. This allows operators to make fast, informed decisions, mitigate risks, and optimise rig time efficiency.
Additionally, the SonicSync™ Wireless Command+Control Platform—typically used to program downhole data sampling schedules—can also transmit wireless surface-to-downhole signals to trigger third-party fluid samplers or decode downhole-to-surface signals for positive perforation gun firing confirmation, enhancing operational control and reliability.
Advancements in well design, including higher deviation angles and tighter build-up rates, have introduced greater complexity in achieving precise subsurface targets and maximising reservoir contact. These factors result in narrow mud weight windows, necessitating accurate and timely measurements. When productivity is a key objective, rigorous sand control and stimulation treatment pumping schedules must be carefully monitored in terms of displacement pressures and equivalent circulating densities.
As continuous circulation of a single-phase fluid cannot be maintained during completion operations, post-job data analysis alone is insufficient to accurately estimate real-time conditions. Traditional pressure pulse technology fails to deliver timely and adequate downhole pressure and temperature data unlike the SonicGauge™, which can serve as the backbone of sand control placement operations.
The SonicGauge™ enables cost-effective regulatory compliance by delivering high-resolution downhole data to detect deviations from expected subsurface storage pressures. The technology dynamically measures injection and production pressure gradients through SonicRepeater stations equipped with onboard sensors, strategically deployed along the tubing string to ensure operational safety while attaining optimum storage capacity.
Under Development: Given that high injection and production rates can induce tubing oscillations, enhancements to the current technology could extend beyond pressure and temperature monitoring to provide real-time vibration data. This advancement would elevate the operation of gas storage facilities, enhancing safety and system integrity management.
The SonicGauge™ can be deployed below mechanical plugs, storm packers, inflatable packers or metal-alloy barriers to deliver real-time differential pressure data during pressure testing and continuous monitoring of above- and below-plug conditions over multi-year periods. This ensures early detection of barrier degradation, enhances well integrity assurance, and provides operators with the data required to make informed decisions about well suspension and abandonment strategies.
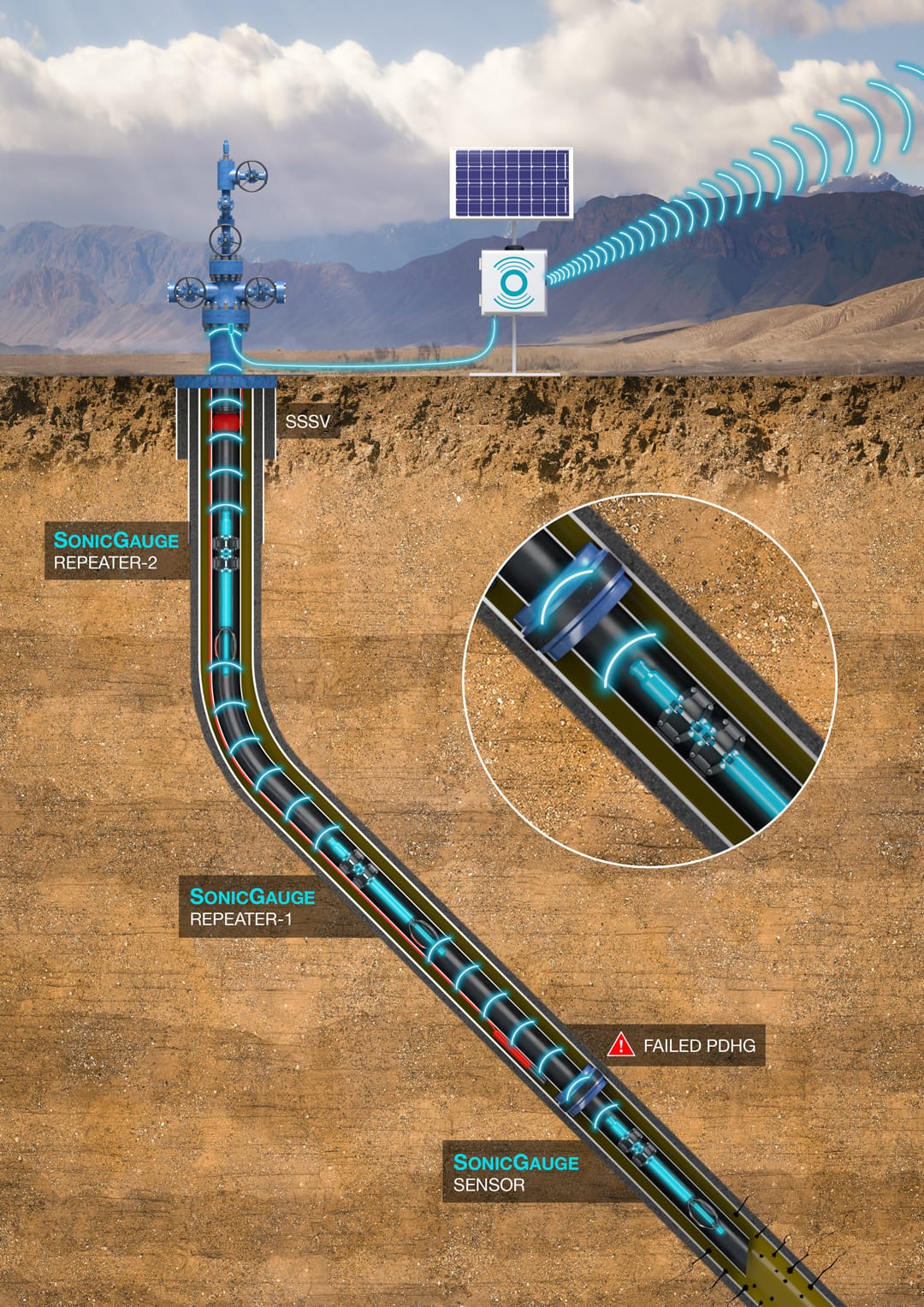
DEPLOYMENT OPTIONS
Designed to match the SonicGauge™ 1.31” slimline profile, the Barracuda™ has been the only solution on the market since 2019 capable of deployment in 2-3/8” or larger production tubing ODs. It offers the least flow restriction of any rig-less data acquisition tool, outperforming high-expansion devices, lock mandrels, and tubing stops. The pressure drop across the compact toolstring is minimal—typically in the order of a couple of psi—making it ideal for a wide range of production wells.
SURFACE OPTIONS
SPECIFICATIONS
SONICGAUGE™ WIRELESS MONITORING SYSTEM | |
---|---|
Sampling Rate | From 1 Second to Hourly Data |
Battery Life | Up to 8 Years (Incl. 20% Safety Factor) |
Communication Type | Two-Way Mesh Network (Controlled by SonicSync™) |
Transmission Distance | Unlimited with SonicRepeaters (Providing Gradient Data) |
Downhole Sensor | Piezo | Quartz (Incl. Multi-Sensor Configuration) |
Temperature Rating (Max.) | 150°C (302°F) |
Pressure Rating Options (Max.) | 10,000 | 15,000 | 25,000psi |
SonicGauge™ Dimensions | L: 1300–1800mm (51.2–70.9") | OD: 33.4mm (1.31") |
Barracuda™ HEX-Hanger™ Dimensions | L: 650–950mm (25.6–37.4") | OD: 33.4mm (1.31") |
Barracuda™ Electro-SET™ Dimensions | L: 590–820mm (23.2–32.3") | OD: 47.3–54mm (1.862–2.125”) |